Beyond the Giants (19)
- murakami26
- Oct 5, 2022
- 3 min read
Updated: Oct 12, 2022
Conditions for survival in the manufacturing industry in VUCA era
Satoru Murakami CEO Goal-System consultants Inc.,
It gets complicated as it gets bigger
Last time, I examined what part of Toyota's TPS has evolved with reference to changes in the environment, the invariant "principle" and the "action" that should change. From this time on, let's think about how to confront VUCA, which is the environment of today.
First, let's think about "complexity". We have been fighting complexity for a long time. As I introduced, the big manufacturing competition that started in the 1920s started with one Ford T-type Ford variety. After that, GM succeeded in a full line strategy by increasing the variety of products, and Toyota created a mixed flow line of various products. Dr. Goldratt (TOC) stood on the shoulders of Giants and tried to handle a wide variety of small quantities with a DBR (drum buffer rope) that simplified the Kanban method.
As the economy develops, many companies emerge and the world becomes more and more complex in order to meet the different needs of many enriched customers.
So what does it mean to be "complex"? This can be easily understood by considering that many elements move apart.
The degree of complexity depends on the number and type of elements, and the greater the number and type of elements, the greater the complexity. In general, when there are many elements, we take an approach that separates them into individual elements, recognizes them, and responds individually. However, the seemingly unrelated elements are often causally linked to each other, and even if they are dealt with separately, they often do not lead to a fundamental solution to the problem.
"For complexity, we divide the entire system into many subsystems, aiming to maximize individual performance as if they were independent units, which is an organization. Dr. Goldratt warns that it will spread harmful partial optimization to the whole.
In general, we divide work into departments according to the organizational structure of each function, and we strive to maximize the performance by deciding the scope of responsibility for each department.
However, he points out that the more he does, the more he prioritizes his own convenience and concentrates on what is in front of him, creating a silo-type organization and calling for partial optimization.
Let's think about how to challenge complexity in today's environment, while tracing how Toyota's Ohno et al. And TOC's Dr. Goldratt approached complexity. Kiichiro Toyoda, the founder of Toyota, has set the ideal that "the ideal of manufacturing is a state where machines, equipment, people, etc. that the idea of "just in time" to eliminate waste.
This was a precursor to the idea of continuous improvement, which is to solve daily problems on the spot and bring them closer to the ideal, but as the times progress and the needs of the market and customers diversify, the problems become very diverse and each. It is said that the relationship between the two was intricately intertwined, and it became extremely difficult to solve the problem, and the situation was such that waste(MUDA) was producing another waste(MUDA).
In order to overcome this situation, Mr. Ohno and his colleagues combined an information gathering method called "three-why principle", in which people see the actual thing in the field and know the reality, and an approach of asking "why why" and finding the root cause. Then, I devised a way to find out the true cause of things (Root Cause).
Mr. Ohno explains the importance of asking "why" by taking the problem of "machine stopped" as an example. … “Toyota Production Method”: From Taiichi Ohno
When a machine in a factory breaks down and stops, the question "Why did the machine stop?"
"The fuse was blown due to overload" If you just answer, you will only get the answer that you should replace the fuse and restart. But the question of why it was overloaded
This is because the bearings are not sufficiently lubricated. And further analyzed
The lubrication pump has not pumped up oil sufficiently.
The shaft of the pump is worn and rattled.
Since the filter was not attached, the facets entered the lubricating oil.
If you go all the way to this point, you will understand the true cause of the problem. Therefore, if a filter is installed in the oil circulation system, it is possible to permanently prevent the trouble that the machine often stops.
This is what Mr. Ohno calls a scientific analysis based on facts to find out the root cause. In this way, Mr. Ohno thoroughly looked at the reality in the field and stuck to "visible solutions".Because, Mr. Ohno thought that it is very important to clarify the causal relationship, clarify the connection between the elements, and decide the point (root couse) to be dealt with for "complexity".
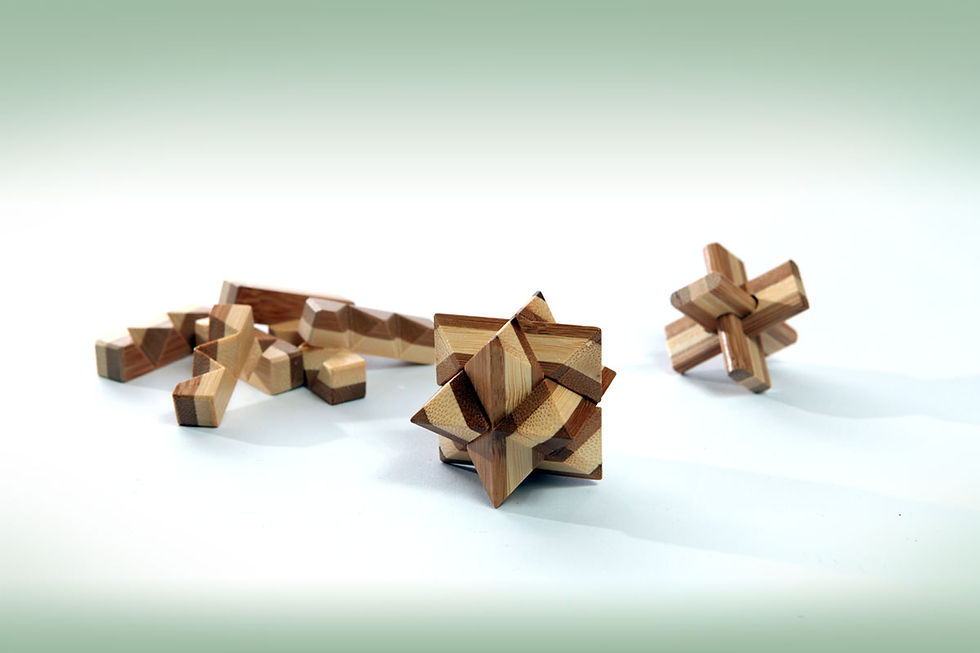
Comments